Maximizing Efficiency and Performance of Diesel Generators for Inductive Loads
Introduction
Diesel generators play a crucial role in providing backup power during outages or in remote locations where grid power is unavailable. In many industrial and commercial settings, these generators are essential for powering equipment and machinery, especially when dealing with inductive loads. Inductive loads are common in applications that involve motors, transformers, and other devices that rely on electromagnetic induction for operation. However, these loads present unique challenges for diesel generators due to their reactive power requirements and the potential for voltage fluctuations and power surges. In this article, we will explore the considerations and best practices for optimizing the performance and efficiency of diesel generators when powering inductive loads.
Understanding Inductive Loads
Before delving into the specifics of diesel generator operation with inductive loads, it is essential to understand the characteristics of these loads. Inductive loads are devices that store energy in the form of a magnetic field when current flows through them. Examples of inductive loads include electric motors, transformers, solenoids, and induction heating equipment. When these devices are connected to a power source, they exhibit reactive power consumption, which is distinct from the active power used to perform useful work.
The reactive power component in inductive loads results in a phase shift between voltage and current, leading to power factor issues. Power factor is a measure of how effectively electrical power is converted into useful work, with a perfect power factor of 1 indicating all power is being used for work. In the case of inductive loads, the power factor is typically less than 1, which means that a portion of the supplied power is not utilized efficiently.
Challenges Faced by Diesel Generators with Inductive Loads
When diesel generators are tasked with powering inductive loads, several challenges can arise that impact performance and efficiency. These challenges include:
1. Starting Current: Inductive loads require a higher starting current compared to their operating current. This surge in current can strain the generator and lead to voltage drops, potentially affecting other connected equipment.
2. Voltage Fluctuations: The reactive power demands of inductive loads can cause voltage fluctuations and instability in the generator output. Rapid changes in voltage levels can damage sensitive electronics and disrupt the operation of equipment.
3. Power Factor Correction: Diesel generators typically operate at a fixed power factor, which may not align with the reactive power requirements of inductive loads. This mismatch can result in inefficient power delivery and increased fuel consumption.
4. Harmonics: Inductive loads can introduce harmonics into the electrical system, causing distortion in the waveform and affecting the quality of power supplied by the generator. Harmonics can lead to overheating of equipment and reduce overall system efficiency.
Strategies for Optimizing Diesel Generator Performance with Inductive Loads
To overcome the challenges associated with powering inductive loads, diesel generator operators can implement various strategies to enhance performance and efficiency. These strategies involve a combination of equipment selection, system design, and operational practices aimed at maximizing the generator's capability to handle reactive power demands effectively. Some of the key strategies include:
1. Proper Sizing: Selecting a diesel generator with adequate capacity to handle the starting current requirements of inductive loads is essential. Oversizing the generator can lead to inefficient operation, while undersizing can cause voltage instability and potential damage to the generator.
2. Power Factor Correction: Implementing power factor correction devices such as capacitors can help offset the reactive power demands of inductive loads and improve overall system efficiency. By adjusting the power factor closer to unity, the generator can deliver power more effectively to the connected loads.
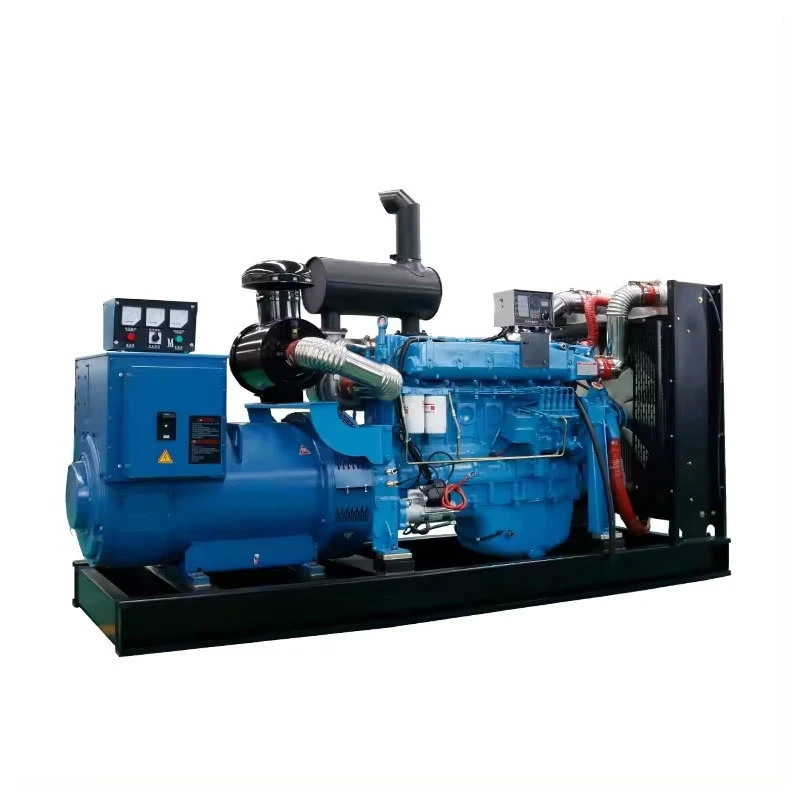
3. Voltage Regulation: Utilizing voltage regulators or automatic voltage control systems can help mitigate voltage fluctuations caused by inductive loads. These devices ensure a stable output voltage, preventing damage to equipment and maintaining system reliability.
4. Load Management: Implementing a load management strategy that prioritizes the sequencing of inductive loads can reduce the impact of starting currents on the generator. By staggering the startup of multiple devices, the generator can handle the load more effectively and prevent voltage drops.
5. Monitoring and Maintenance: Regular monitoring of generator performance and conducting preventive maintenance are crucial for ensuring optimal operation with inductive loads. Monitoring parameters such as voltage, current, power factor, and harmonics can help identify potential issues early and prevent system failures.
Case Study: Diesel Generator Application in an Industrial Setting
To illustrate the practical implementation of diesel generators for inductive loads, let's consider a case study of a manufacturing plant that relies on several electric motors for its production processes. The plant experiences frequent power outages due to grid instabilities, necessitating the use of a diesel generator as a backup power source.
The electric motors used in the plant exhibit high starting currents and reactive power requirements, posing a challenge for the diesel generator to maintain stable power delivery. To address go now , the plant management implements the following strategies:
1. Proper Sizing: A diesel generator with a capacity exceeding the cumulative starting current of all motors is selected to ensure reliable operation during startup sequences.
2. Power Factor Correction: Capacitor banks are installed to compensate for the reactive power demands of the electric motors, improving the overall power factor of the system.
3. Voltage Regulation: Automatic voltage regulators are integrated into the generator system to stabilize the output voltage and prevent fluctuations during load changes.
4. Load Management: A sequential startup protocol is established to control the energization of electric motors, reducing the instantaneous demand on the generator and minimizing voltage drops.
5. Monitoring and Maintenance: Regular inspections and performance monitoring of the diesel generator system are conducted to identify any issues promptly and ensure optimal operation under varying load conditions.
By implementing these strategies, the manufacturing plant successfully enhances the efficiency and reliability of its diesel generator system when powering inductive loads. The combination of proper equipment selection, system design, and operational practices enables the plant to maintain uninterrupted production processes even during power interruptions.
Conclusion
Diesel generators are versatile power sources that can effectively handle the challenges posed by inductive loads in various applications. By understanding the characteristics of inductive loads and implementing appropriate strategies, operators can optimize the performance and efficiency of diesel generators in powering such loads. Proper sizing, power factor correction, voltage regulation, load management, and monitoring are key elements in ensuring reliable operation and minimizing downtime in industrial and commercial settings.
As the demand for backup power solutions continues to grow, the importance of maximizing the capabilities of diesel generators for inductive loads becomes increasingly evident. By adhering to best practices and staying abreast of technological advancements in generator systems, operators can achieve optimal performance and longevity from their diesel generator investments. Effective management of inductive loads with diesel generators not only enhances operational efficiency but also contributes to overall system resilience and stability in diverse power scenarios.